複雑に組み上げたExcelで管理。生産計画の変更が頻発し臨機応変な対応が必要なため一日中PCに張り付いていた。
現状の計画を反映するのに精一杯でマネージャーが生産管理以外の仕事が手につかない状況。
事例
弊社の変化と他社の事例をご紹介します。
- 自社ブランドデニム製造
株式会社総社カイタックファクトリー Excel管理からの解放
マネージメント時間の確保へ
Excel管理
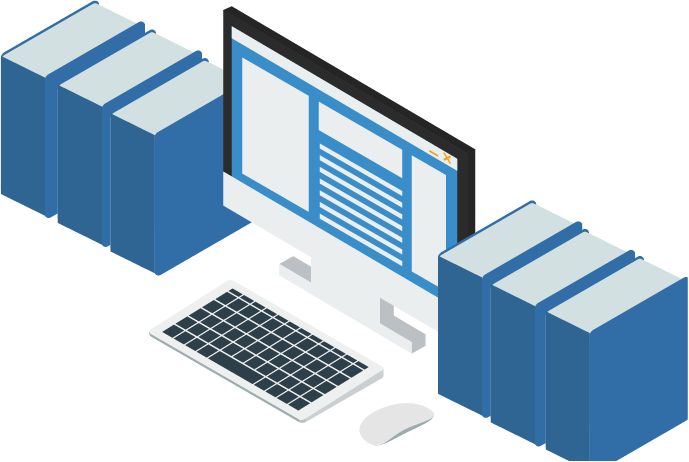
生産管理システム
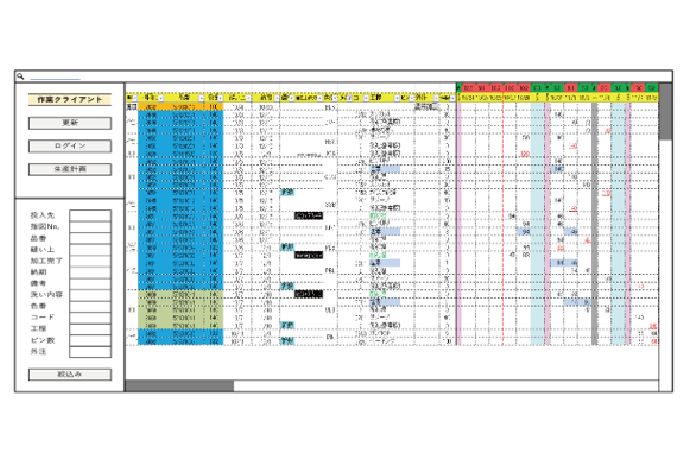
生産管理システムを導入することでオペレーションがシンプルになり、生産管理の効率化はもちろんマネジメント業務を行う時間が確保できるように。
- 自社ブランドデニム製造
株式会社総社カイタックファクトリー 動画分析から機械の稼働率の偏りを発見
業務の効率化へ
偏った稼働率
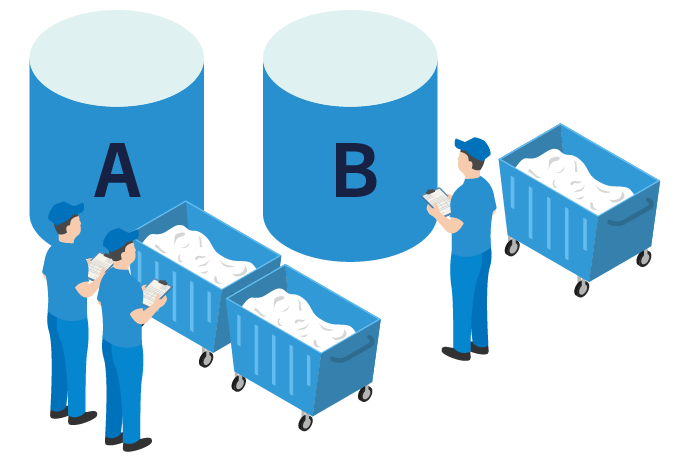
デニムの洗い工程に使用される2台の窯で稼働率に大きな差があった。
※洗釜A、Bは同じタイプのサイズ違いの窯
洗釜A: 80%
洗釜B: 30%
稼働率の差を改善
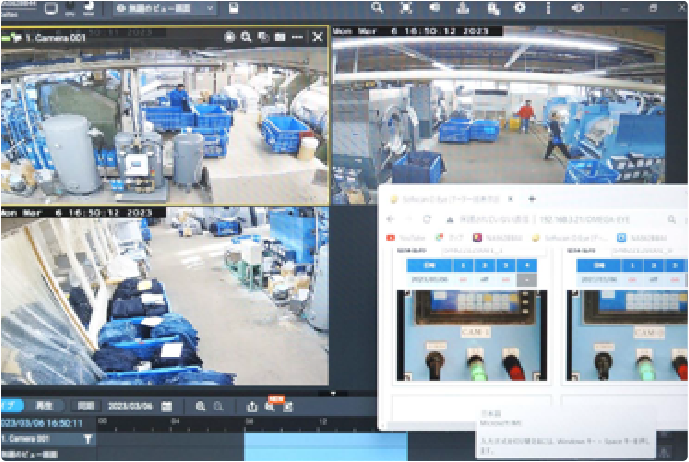
データを明確に示したことで洗釜A、洗釜Bの使用率の差が改善。
現場スタッフが全力で働いている中で見えていない課題を数値で洗いだすことができた。
- 制御盤製造
東洋電装株式会社 生産性向上と
35.6%の無駄削減
工具を共有
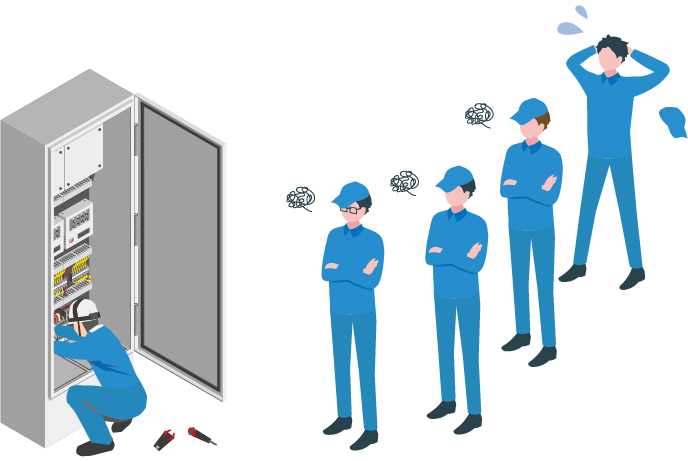
作業の動画分析から、工具を共用することで移動の無駄があることが分かりました。
①取りに行って戻す移動
②他の作業者が使用中には待たなくてはいけない
作業者一人一人に支給
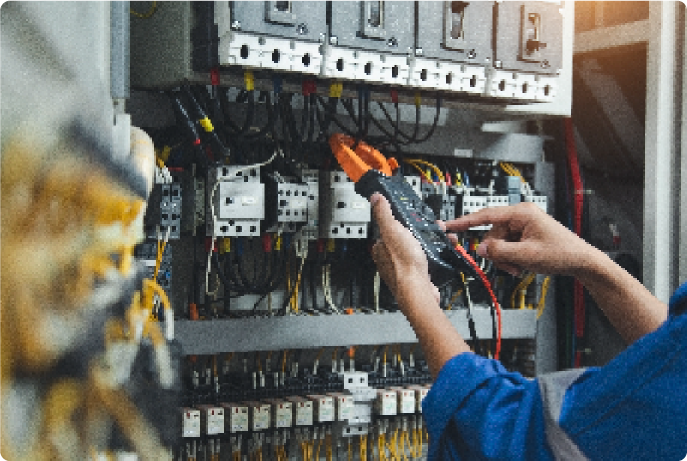
高価な工具を共有使用している中小企業は多いですが、動画により職人の動作がデジタル化され、この移動や待ち時間を削減することは、設備投資との比較が可能になりました。
設備投資の費用以上に効果があると判断し一人に一つ工具を用意することで一部の作業における35.6%の無駄を削減に成功しました。
- 制御盤製造
東洋電装株式会社 図面ペーパーレスで
紙資源の削減とスキャン時間短縮
紙の設計図で管理
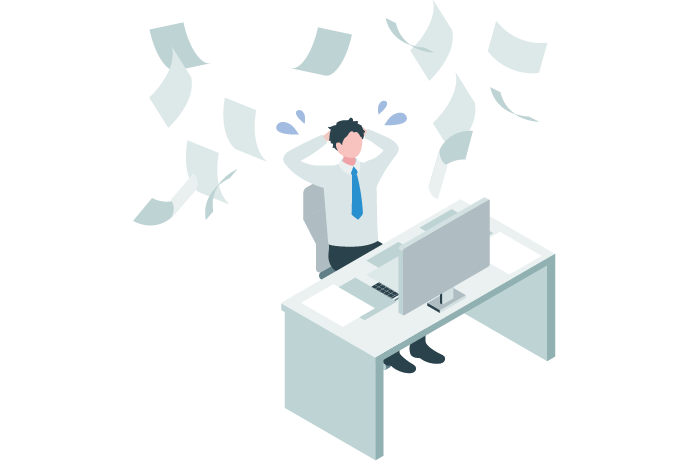
これまで数十枚の図面を設計者や製造担当者が印刷していました。
①製造側での修正を記入して設計と相談
②修正後再印刷
③検査工程でまた印刷して検査結果を図面に記入+スキャンしてデータ化
作業をデータ管理
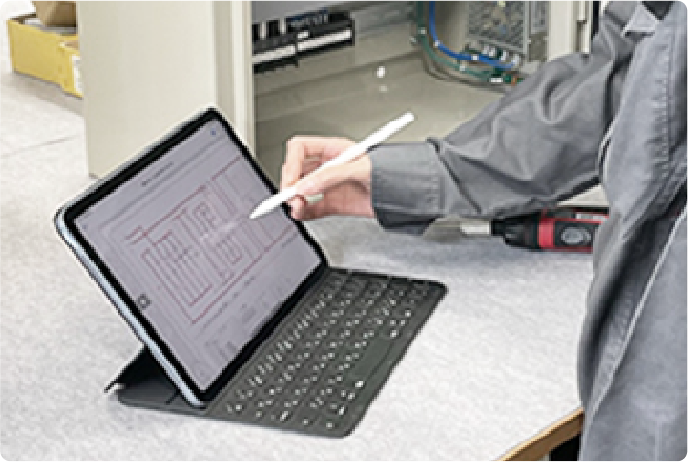
作業をすべてデータ上(PDF)で完了。
また各工程でのメモも紙ではなくデータに残し、大幅な作業の効率化とデータ蓄積、リアルタイムの情報共有を実現しています。
- 制御盤製造
東洋電装株式会社 職人技の発見と作業の明確化
全ての人が同じ作業
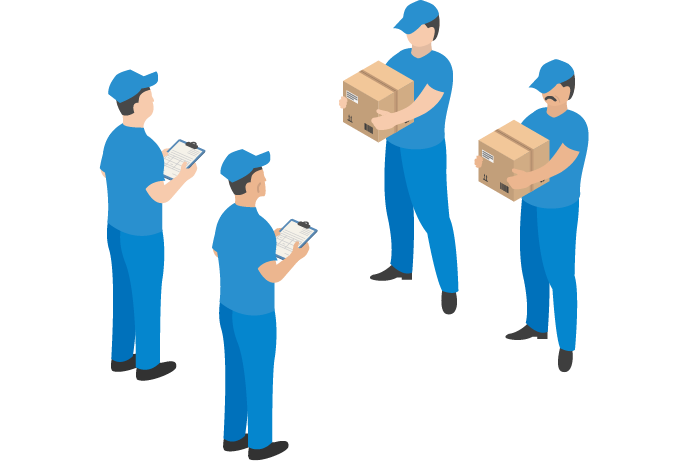
職人にしか難しい作業とロボットや若手でもできる作業を分類して作業の適切な担当者を明確化しました。
制御盤の配線ルートを決めるのは実は、設計者などには難しく、非常に難易度の高い“職人技”です。
適材適所

適材適所で職人が高付加価値の仕事に集中できるように作業の配分を見直しました。