It was managed with a complexly assembled EXCEl. We had to monitor PCs all day long because changes in production plans occur frequently and we have to respond flexibly.
Managers are unable to do any work other than production management because they are doing their best to reflect the current plan.
Case Example
Here are some case examples of our changes and those of other companies.
- Own-brand denim manufacturing
Soja Caitac Factory, CAITAC INTERNATIONAL, INC. To be freed from EXCEL management
Secure your management time
EXCEL Management
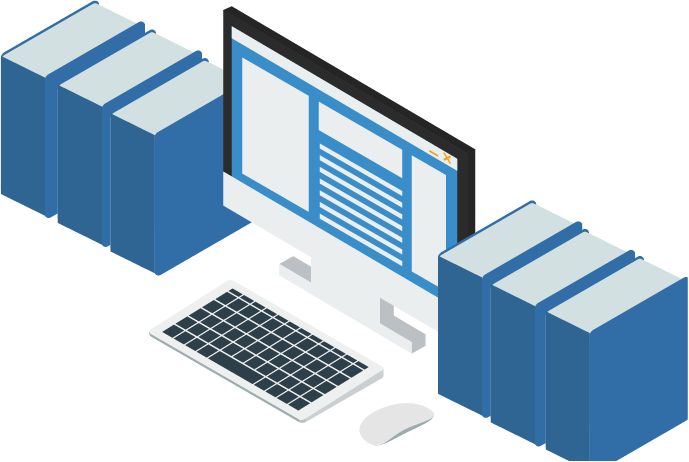
Production Management System
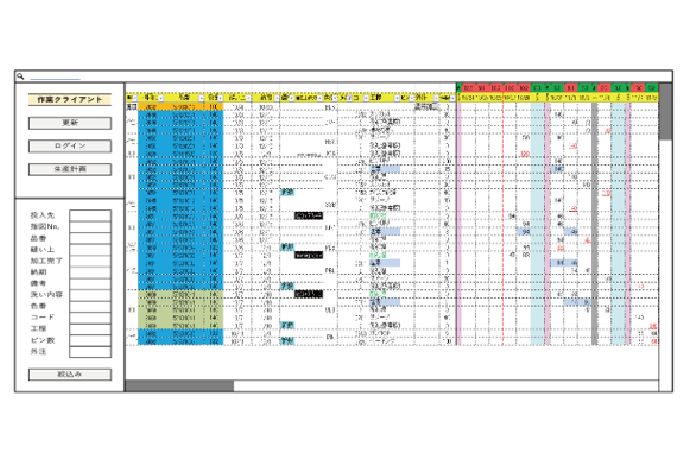
The introduction of a production control system simplifies operations and allows time for management tasks as well as more efficient production control.
- Own-brand denim manufacturing
Soja Caitac Factory, CAITAC INTERNATIONAL, INC. Discover bias in machine operating occupancy rates through video analysis
Improve operational efficiency
Unbalanced operating occupacy rate
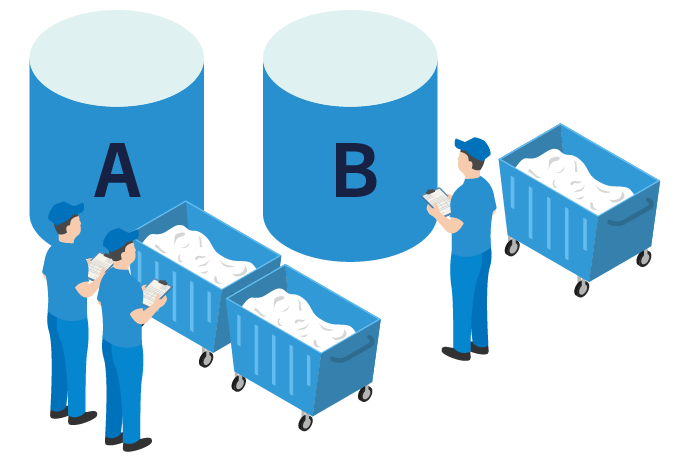
There was a big difference in operating occupancy rates between the two kilns used for the rough denim process.
※Washing kilns A and B are the same type of kiln but different sizes.
Washing kilns A :80%
Washing kilns B:30%
Improve operating occupancy rate differentials
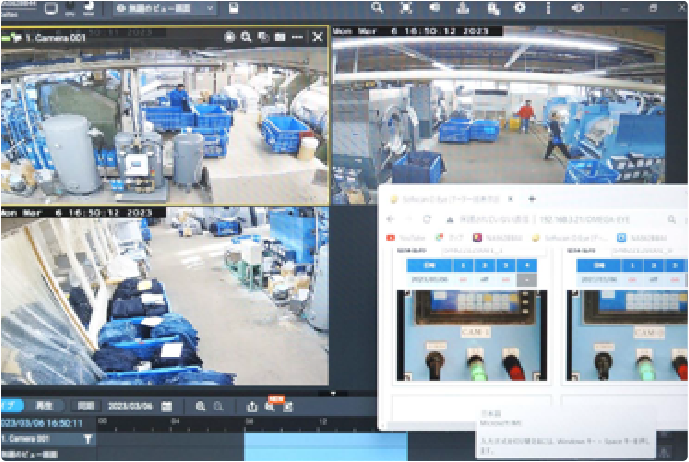
By clearly presenting the data, the difference in the usage rate of washing kilns A and B improved.
We were able to numerically identify issues that were not visible while the on-site staff was working hard.
- Control panel manufacturing
TOYODENSO Co., Ltd. Increased productivity and
35.6% waste reduction
Tools are shared.
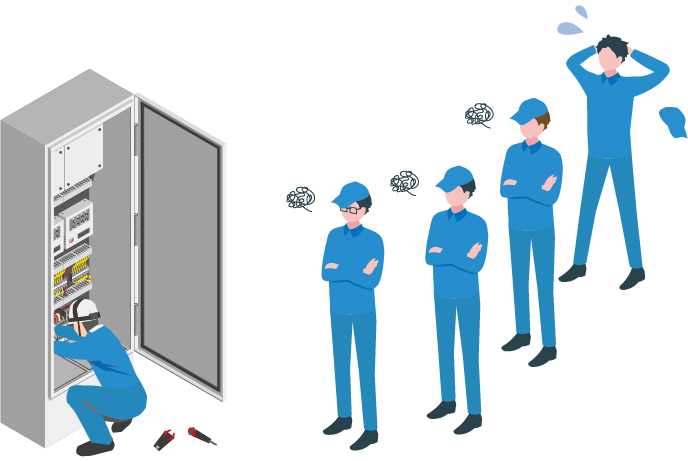
Video analysis of work revealed that sharing tools results in wasted movements.
1.Move to pick up and return the tool.
2.Wait time while other workers are using the tool.
Tools are provided for each worker.
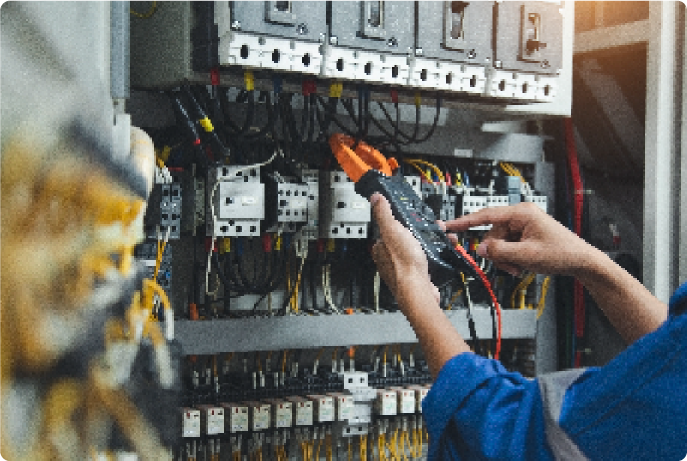
Many small and medium-sized companies share expensive tools, but video digitized the craftsman’s movements, and the reduction of this move and wait time could be compared to the capital investment.
By providing a tool for each person, we succeeded in reducing 35.6% of unnecessary movements in some tasks.
- Control panel manufacturing
TOYODENSO Co., Ltd. Paperless drawings
reduced paper resources and scanning time
Work is managed by paper drawings.
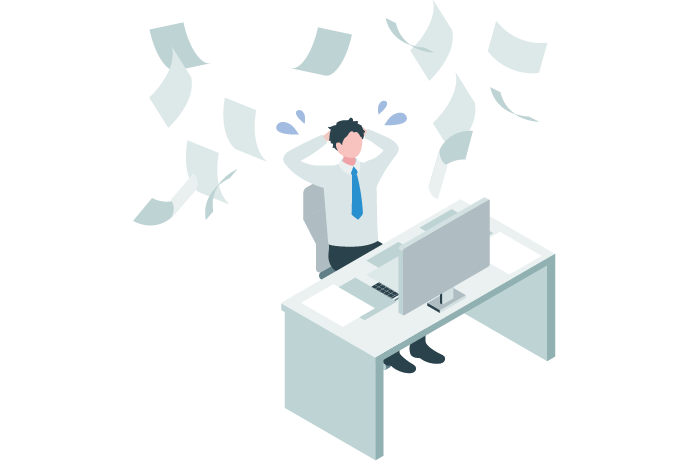
Previously, designers and manufacturing personnel printed out a set of dozens of drawings.
1. Fill in the modifications in drawings by manufacturing side and discuss with designers.
2. Reprint after correction.
3. Printed again in the inspection process and the inspection results are filled in the drawing and scanned into data.
Work is managed by data.
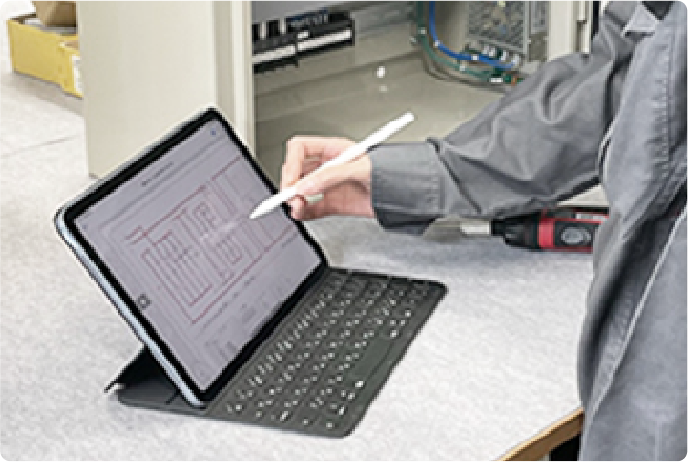
All work is completed on the data (PDF).
In addition, memos at each step of the manufacturing process are kept in data, rather than on paper, to significantly improve work efficiency, accumulate data, and share information in real time.
- Control panel manufacturing
TOYODENSO Co., Ltd. Discovering craftsmanship and clarifying work
Everyone does the same work.
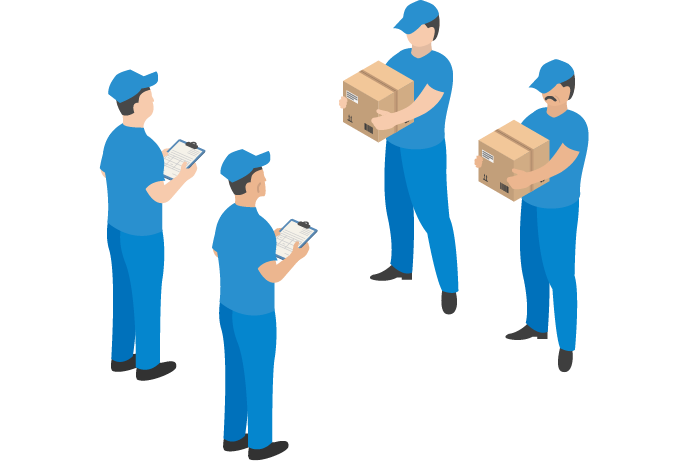
We categorized difficult tasks that can only be done by craftsmen and tasks that can be done by robots or new workers, and clarified the appropriate person in charge of the tasks.
Determining the wiring route of a control panel is actually a very difficult “craftsmanship” that is difficult for designers and others to do.
Right person in the right place.

“Right person in the right place.” means that we have reviewed the distribution of work so that craftsmen can focus on high value-added work by placing the right person in the right place.